In the competitive landscape of wholesale stainless steel tumblers, quality assurance (QA) plays a crucial role in ensuring product reliability, customer satisfaction, and brand reputation. With two decades of experience in both SEO and tumbler sales, I understand that the success of any wholesale business hinges on product quality. This blog will explore the critical aspects of quality assurance in the wholesale stainless steel tumbler market.

Table of Contents
Understanding Quality Assurance
Quality assurance involves systematic processes and procedures to ensure products meet quality standards before they reach customers. For stainless steel tumblers, this means rigorous testing and evaluation at every production stage. Key elements include:
- Material Selection: Using high-quality food-grade 18/8 (304) stainless steel ensures durability and safety. This material resists rust and corrosion, maintaining tumbler integrity over time.
- Manufacturing Standards: Adhering to international standards like FDA and LFGB certifications is essential. These certifications guarantee that tumblers are safe for food contact and free from harmful chemicals like BPA.

The Role of Testing in Quality Assurance
Testing is a key component of QA. Each tumbler must pass a series of tests to ensure it meets performance expectations:
- Durability Tests: Tumblers should withstand everyday use without cracking or fading. Tests also include assessing temperature retention to ensure beverages stay hot or cold for extended periods.
- Leak Resistance: A well-designed tumbler must prevent spills. Quality assurance processes often include pressure testing lids and seals to ensure they work effectively in various conditions.
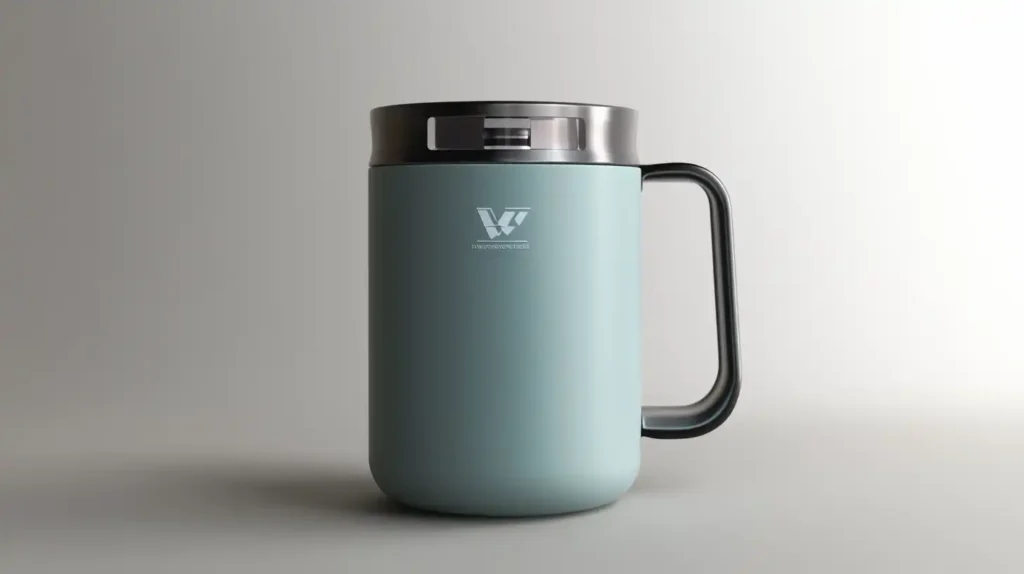
Benefits of Quality Assurance
Implementing a robust QA program offers several benefits:
- Customer Satisfaction: High-quality products lead to happy customers who are more likely to make repeat purchases and recommend your brand. Positive reviews boost online visibility due to SEO algorithms favoring well-reviewed products.
- Brand Reputation: Consistent quality builds trust, positioning your brand as an industry leader. This enables you to command higher prices and foster customer loyalty.
- Reduced Returns and Complaints: Ensuring products meet high standards before reaching customers minimizes returns and complaints, saving costs related to handling returns and refunds.

Conclusion
Quality assurance is not just an operational necessity—it’s a strategic advantage in the wholesale stainless steel tumbler market. By prioritizing QA throughout the manufacturing process—from material selection to final testing—businesses can boost customer satisfaction, build a strong brand reputation, and achieve long-term success. For wholesalers looking to thrive in this competitive market, investing in quality assurance is essential for meeting and exceeding consumer expectations.
By focusing on these principles, wholesalers can ensure their stainless steel tumblers not only meet but exceed market demands, positioning themselves as leaders in quality and reliability within the industry.